One of the challenges of recreating these beautiful tuners is knowing which brass to use.
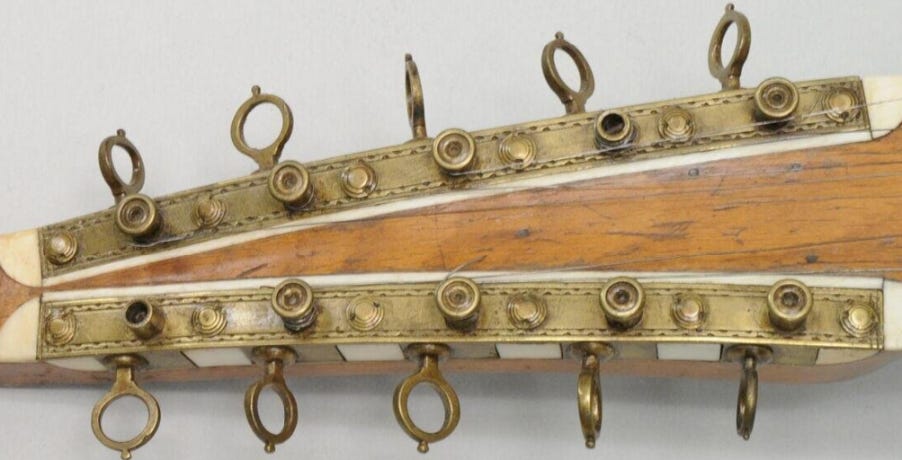
Until recently, I didn’t realise that there was really more than one kind of brass. I managed to use an XRay Fluoroscope at West Dean to analyse the brass in these tuners, that I have been lent to study:
Until the mid 18th Century, brass had a maximum of about 28% zinc. This was because it was created using zinc oxide in a process called cementation. After the middle of the century, zinc itself could be used, creating a higher ratio.
The XRF results are interesting. They show that the frames have 67% copper, 33% zinc and no lead (lead is added to make brass more easily machined). This is quite surprising as this is a very high percentage zinc for the time - the UK patent on smelting zinc and copper was issued in 1781, 18 years after these were created.
The other components are much more typical for the time: around 25% zinc, 73% copper and 1-2% lead.
It turns out that there are different strengths of alloy brass. Up to 38% zinc and the brass is called “alpha” brass because of the microstructures within it. Alpha brass is very soft and easy to work. As a result it is not really suitable for clockwork, gears, cogs, etc.
From 38% to 45% zinc content and the brass is known as “alpha-beta”. This is the goldilocks of brass - neither too hard nor too soft. It is a two-phase alloy as it contains a mixture of the alpha structures and the beta structures. For the pinion gears I’ve made I’ve been using a modern alloy called CZ121 which has roughly 39% zinc, 3% lead and 58% copper. This fits perfectly into the alpha-beta range. Beyond 45% and the brass becomes beta brass which is very hard and cannot be worked without heat.
I’ve successfully made a prototype using CZ121 brass by cutting the pinion on a lathe and hand cutting the worm with a hacksaw and then cleaning up with files.
Understanding all this about brass has thrown a wobbly into my plan to cast the worm gears: unfortunately it is very hard to cast alpha-beta brass. This is because the boiling point of zinc (at 907C) is lower than the melting point of copper (1085C). So as you melt the alpha-beta brass, a lot of zinc boils away leaving a much lower percentage of zinc in the final alloy (and also being very poisonous to whoever is doing it!). Basically you start with alpha-beta and end up with alpha…
I’m left with some options:
Forget about casting the worm gear and cut the worm gears on a lathe and then join them to cast heads. Sounds like a slow process! Another option would be to attempt to mill and turn the entire head and worm from solid CZ121 brass which also sounds slow and wasteful.
Try to up the zinc percentage during casting by adding extra zinc and working quickly. This might work but might also leave a rather random result. I’ve been told you have to put the zinc under the brass in the crucible and minimise stirring the molten metal to avoid the zinc precipitating, which may lead to uneven mixtures and good castings and bad castings.
I could give up on brass for the heads and cast them in bronze which is much stronger. This might not look great but may be a good option. I may have to selectively age the brass and bronze components to try to get a colour match. It certainly wouldn’t be authentic.
Another unauthentic but tempting option is to add some silicon into the brass. Silicon makes the alloy much stronger and even with as little as 15% zinc you can get a comparitively hard brass if you add just 4-5% silicon. Silicon has an incredibly high melting point, but does dissolve into molten copper at a lower temperature.
The option I have missed out is to be 100% authentic and make the gears from alpha brass and try to work harden them. This is what I suspect they did in the 18th Century, and as you can see from the tuners above, was not 100% successful. When I talk about this project to people who know about Gibson tuners, the first thing they ask me is - can I repair a set that they have that are broken! I’m not tempted to make a replica that has the same problems as the originals.
I’m going to try some experiments and I’ll update this blog with the results.
In the meantime, here is a short video of Arnaud and I testing my hand cut prototype under tension:
PS I later tested it up to 12 kgs tension (about the tension of a modern steel string on a guitar) and the brass lute string broke, but the tuner was fine.
PPS I’ve been in correspondence with Andrew Dipper who has been doing amazing work on Gerald Trimble’s two Salters. Andrew has been very kind sharing information about the restoration of the tuners, but I have avoided sharing that information here because I know he is currently preparing a monograph and article about the restoration. I’m eagerly awaiting the chance to read them!
My deep thanks to both Andrew and Gerald for their time and help on this project.